Joebob
Goblin Guru
Long time no write.
I have had a few weeks where I had all the prep work done for the donor parts and before my kit arrived. the great news is that last Friday I made it out to Red Oak and picked up my kit!!!
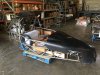
A friend of mine was going to come with me and use his truck but he had house issues and had to back out.
What worked out was I rented a flatbed truck from Home depot. Not the cheapest option but with unlimited miles, worked out well. With the 10 foot bed and the extended chassis, Adam and I can confirm that it fits sideways with literally 1/2" of space for the front nose with the frame contacting the other 3 sides.
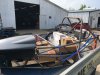
Getting it off the back of the truck was an adventure. I bought a winch to pull the hoses through but repurposed it to lift the frame off the back of the truck. I built a frame for the winch to span several attic joists and drilled a hole in the attic floor to lower the hook through. I backed the truck unto the garage as far as it would go and roped the frame to the hook. Cranked it up, drove the truck out, and lowered it to the ground safely while the wife kept it from swinging. Went very smooth.
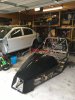
Driving there and back of over 500 miles was exhausting and got the frame unloaded and the truck returned to Home Depot 5 minutes before they closed for the day. Super win.
My fist thought...."Gosh it is so small!!"
With my order I got a couple of options and upgrades:
As I have an automatic transmission and no clutch bracket, I got the Goblin AT diagonal frame braces. This should strengthen and increase torsional rigidity in the frame. I also got the thicker aluminum floor from the AT as well, since we are so low to the ground and I plan to mostly street drive the goblin, I wanted a bit stronger floor for road debris intrusion protection. No pictures as it looks like the regular floor.
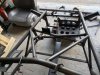
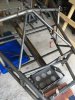
Also upgraded is the thicker lower upright brackets where you can see the increase in thickness as well as material around the bolt holes. This should keep the Goblin tracking straight incase I hit a pothole or something. Cheaper than a new alignment.
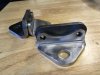
Rounding out the front steering parts is the HD steering arms. Here they are next to the stock arms. They are a little bit thicker and wider and not as deep scallops, and I LOVE the machining on them. Just a piece of mind part as it is available.
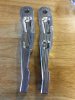
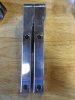
Lastly is the Catted exhaust. As a Texas Goblin with new rules of dubious enforcement, I will set up to be full emission compliant. So rather than figuring out how to make a catted exhaust, DF fabbed me up one.
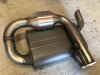
Next step is to find out where to get the frame powder coated and figure out if I need to change anything on the frame to attach Lexan side panels.
I do have one question from the recent kit deliveries: I see that the calipers are silver coated instead of raw cast iron. Do these need to be painted to prevent rusting or do they hold up on their own?
The build starts!!
Joe
I have had a few weeks where I had all the prep work done for the donor parts and before my kit arrived. the great news is that last Friday I made it out to Red Oak and picked up my kit!!!
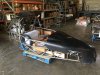
A friend of mine was going to come with me and use his truck but he had house issues and had to back out.
What worked out was I rented a flatbed truck from Home depot. Not the cheapest option but with unlimited miles, worked out well. With the 10 foot bed and the extended chassis, Adam and I can confirm that it fits sideways with literally 1/2" of space for the front nose with the frame contacting the other 3 sides.
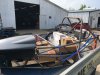
Getting it off the back of the truck was an adventure. I bought a winch to pull the hoses through but repurposed it to lift the frame off the back of the truck. I built a frame for the winch to span several attic joists and drilled a hole in the attic floor to lower the hook through. I backed the truck unto the garage as far as it would go and roped the frame to the hook. Cranked it up, drove the truck out, and lowered it to the ground safely while the wife kept it from swinging. Went very smooth.
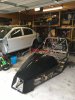
Driving there and back of over 500 miles was exhausting and got the frame unloaded and the truck returned to Home Depot 5 minutes before they closed for the day. Super win.
My fist thought...."Gosh it is so small!!"
With my order I got a couple of options and upgrades:
As I have an automatic transmission and no clutch bracket, I got the Goblin AT diagonal frame braces. This should strengthen and increase torsional rigidity in the frame. I also got the thicker aluminum floor from the AT as well, since we are so low to the ground and I plan to mostly street drive the goblin, I wanted a bit stronger floor for road debris intrusion protection. No pictures as it looks like the regular floor.
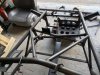
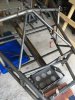
Also upgraded is the thicker lower upright brackets where you can see the increase in thickness as well as material around the bolt holes. This should keep the Goblin tracking straight incase I hit a pothole or something. Cheaper than a new alignment.
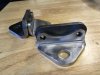
Rounding out the front steering parts is the HD steering arms. Here they are next to the stock arms. They are a little bit thicker and wider and not as deep scallops, and I LOVE the machining on them. Just a piece of mind part as it is available.
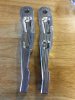
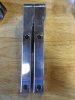
Lastly is the Catted exhaust. As a Texas Goblin with new rules of dubious enforcement, I will set up to be full emission compliant. So rather than figuring out how to make a catted exhaust, DF fabbed me up one.
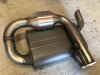
Next step is to find out where to get the frame powder coated and figure out if I need to change anything on the frame to attach Lexan side panels.
I do have one question from the recent kit deliveries: I see that the calipers are silver coated instead of raw cast iron. Do these need to be painted to prevent rusting or do they hold up on their own?
The build starts!!
Joe